“Sloppy notes kill lean.”
“Sloppy notes kill lean.”
Overview and Strategic Vision
In the intricate dance of manufacturing operations, precise meeting documentation forms the backbone of operational success. Industry benchmarks such as SAP’s material requirements planning demonstrate the importance of accurate meeting notes to ensure seamless inventory control and production scheduling. Real-world cases from Toyota and General Electric reveal that systematic documentation integrated with robust CRM systems can catalyze streamlined operations and enhance overall efficiency.

Documentation Challenges in Complex Environments
Meeting notes plagued by neglect or imprecision often lead to miscommunication and process delays. ISO insights on quality management highlight that discrepancies and data quality issues can trigger operational inefficiencies, forcing teams into reactive crisis management modes. Without rigorous documentation protocols, cross-functional teams risk falling behind in an ever-demanding operational landscape.
Empowering Efficiency with Actionable Documentation
Combining expert opinions with data-driven strategies reveals effective methods for merging meeting notes with CRM systems. By incorporating error-checking and data mapping steps, manufacturers can ensure clean data flows directly into their ERP/CRM tools. Case studies—such as those discussed in Google Cloud Gen AI use cases and Indeed’s workflow optimization guidance—offer replicable templates designed specifically for manufacturing setups.
More on Workflow Integration
A typical micro-level workflow starts with clear note-taking, followed by systematic error-checking before the information is automatically fed into the company’s CRM. This reduces manual entry errors and enhances overall data quality, ensuring that operational decisions are backed by reliable information.
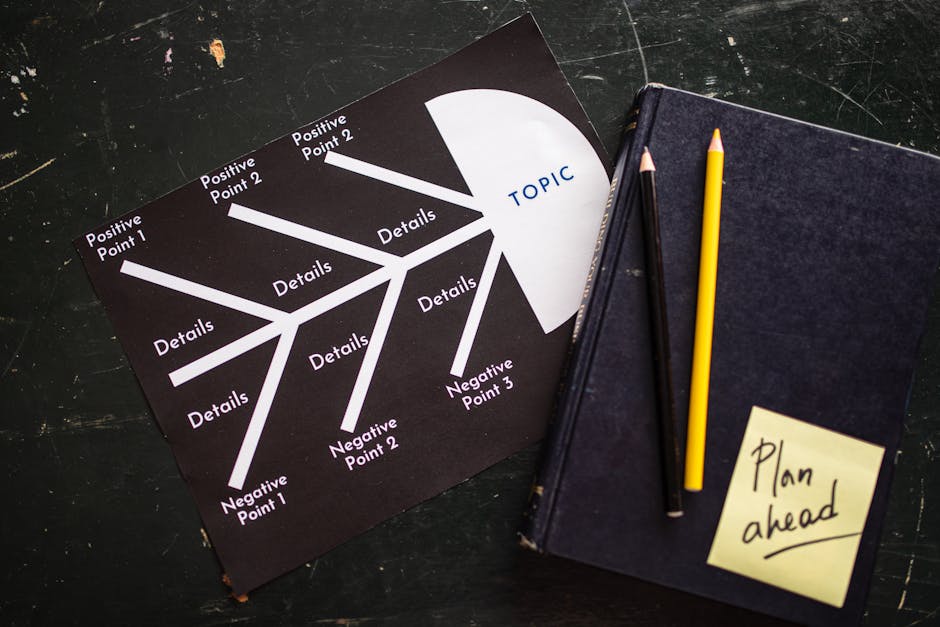
CRM Integration as a Catalyst for Transformation
Linking strategic meeting insights directly to CRM data can significantly accelerate decision-making while minimizing operational silos. By adopting data-driven frameworks, manufacturers can witness real-time corrections and proactive oversight, which in turn bridge the gap between strategic objectives and on-ground executions. This integration not only enhances data fidelity but also promotes a culture of accountability across departments.
Aspect | Old Note-Taking Habits | Precision-Driven Notes |
---|---|---|
Accuracy | Often imprecise and incomplete | Verified and comprehensive |
Integration | Manual transfers and delays | Seamlessly automated with CRM systems |
Efficiency | Time-consuming and error-prone | Streamlined and data-rich |
Impact | Limited operational insight | Drives proactive adjustments and strategic planning |
Considerations: Operational efficiency, error reduction, and data accuracy. Keywords: meeting note to CRM, workflow optimization. |
Future-Proofing and Best Practices
Looking ahead, embedding rigorous meeting documentation within modern CRM systems is key to maintaining a competitive edge. Lean documentation techniques—such as regular audits, periodic integration reviews, and user-centric guidelines—minimize manual reconciliation and errors. Maintaining cross-functional checklists plays a crucial role as a secondary quality control measure.
- Lean Documentation Techniques
- Strategies that streamline meeting notes for seamless integration with ERP/CRM systems, reducing manual reconciliation and enhancing reliability.
- Cross-Functional Checklists
- Routine checklists used as a secondary review to catch data discrepancies and prevent cascading operational inefficiencies.
By adopting these best practices, manufacturers not only curtail error margins but also fortify cross-departmental collaboration—ensuring that every note taken drives the process toward precision and operational excellence.