- MES Integration
- Seamlessly connecting manufacturing execution systems with automated operations to drive real-time KPI monitoring.
- Downtime Analytics
- Tools and data processes that identify, assess, and alleviate production downtimes, ensuring optimal workflow continuity.
- Predictive Maintenance
- Leveraging AI and sensor data to forecast equipment failures and schedule timely maintenance, minimizing unexpected disruptions.
From Floor to Cloud: Real-Time Wins
[08:45] Shift Start
Introduction
The manufacturing sector has entered an era defined by rapid technological integration. Industrial entities are leveraging automation to address KPI drift and streamline reporting processes. Intelligent systems not only enhance team efficiency but also revamp traditional management of key performance indicators. As operations shift from manual to automated workflows, the transformation has become measurable and impactful.
Real-World Case Studies
Major industry players such as Rockwell Automation and JR Automation illustrate the potential of advanced automation technologies. For example, Rockwell Automation has recalibrated its KPI monitoring via real-time dashboards and automated alerts. This integration of technology and human insight has delivered granular control over operational metrics. Similarly, JR Automation’s solutions have helped global manufacturers optimize production and witness concrete shifts in productivity metrics across diverse markets.
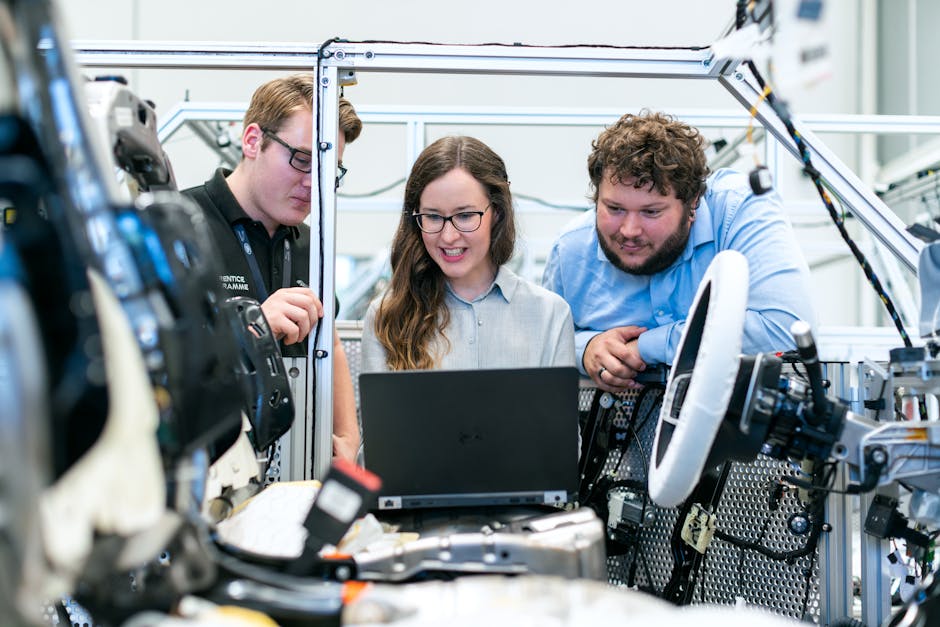
Overcoming Internal Doubts
Many organizations have encountered hesitation with internal builds that delivered minimal returns and skepticism surrounding AutoML. However, industry pioneers have demonstrated that meticulous adjustment of forecasting models through iterative adjustments and performance dashboards is essential for restoring confidence. AI-driven automation, when fine-tuned, has steadily reversed the trend of declining trust in performance metrics.
AI’s Impact on Operational Efficiency
Manufacturers are experiencing directly measurable benefits by reducing manual interventions while embracing advanced robotics and CNC systems. Companies like FANUC America have spearheaded this initiative, systematically reducing downtime through performance dashboards and data-driven approaches. These adjustments have resulted in improved cycle times and enhanced quality assurance, showcasing the tangible impact of AI integration on operational efficiency.
Innovative Tools and Strategies
Precision Automation Inc. provides a prime example of smart adoption of technology. Their strategy involves leveraging adaptive, unsupervised machine learning techniques to detect anomalies in sensor data. By reconciling historical metric discrepancies with novel analytics, these tools allow manufacturers to predict issues before they impact production workflows. This forward-thinking approach is transforming how performance is managed, moving from reactive to proactive strategies.
Learn More: A Closer Look at Adaptive Machine Learning Techniques
Adaptive machine learning can refine predictive maintenance by continuously learning from sensor data. With unsupervised methods, models adjust without human intervention, ensuring the system adapts to new operational patterns. This means anomalies are caught in real time, reducing error rates and supporting more robust reporting mechanisms in an environment where each second of downtime counts.
Tackling Manual Reporting and Model Drifts
The transition from manual reporting to automated, real-time updates has transformed modern manufacturing. Teams have restructured their processes to prioritize clarity and efficiency. Automated reporting dashboards, which update metrics instantly, ensure that KPIs are both accurately monitored and swiftly adjusted in response to variances in operations. This streamlined approach allows manufacturing teams to focus on precision and productivity rather than cumbersome manual processes.
Aspect | Manual Workflow | Automated Workflow |
---|---|---|
Time | Lengthy, prone to delays | Rapid, real-time updates |
Error Rate | Higher risk due to human error | Significantly reduced inaccuracies |
Scalability | Limited by workforce and resources | Easily scaled with technology |
Data Consistency | Variable reliability | High consistency and dependability |
Considerations: For further comparisons on efficiency gains and reporting accuracy, explore industry case studies and automated system analyses in related manufacturing technology resources. |
Conclusion and Key Takeaways
Evidence shows that automation is indispensable in achieving manufacturing excellence. From Rockwell Automation's real-time dashboard integrations to FANUC America's systematic downtime reductions, the application of AI-driven automation has restored trust and accuracy in performance metrics. By replacing manual efforts with precision technology, companies are not only modernizing their operations but are also setting new benchmarks for efficiency in the manufacturing industry.
The insights presented here emphasize that embracing automation is key to overcoming traditional challenges in KPI drift and operational delays. Manufacturers ready to move from reactive systems to proactive performance management can build a more responsive, accurate, and sustainable production environment.