Unlocking Efficiency in Manufacturing Operations
Overview of the Efficiency Imperative
The contemporary manufacturing landscape demands efficiency, driving operations to speed up reporting and sharpen fine-tuning processes. Advanced AI tools and automated report configurations have shifted from speculation to essential industry practices. Technologies pioneered by giants like IBM watsonx.ai are a testament to the tangible impact of these innovations. This discussion grounds its insights in real-world scenarios and technical details, emphasizing that efficiency is a non-negotiable imperative in modern manufacturing.
Deconstructing Operational Challenges
Manufacturing enterprises face complex challenges in report generation and process adjustments. Past efforts to enhance report formats often led to cumbersome overhauls with outputs that lacked accountability. By implementing measures such as audit trails and exception flags, industry leaders have learned to bypass repetitive rebuilds and secure operational ownership. These challenges have paved the way for refined strategies that balance speed with precision.
Case Studies and Expert Insights
Notable examples from organizations like General Electric and Siemens highlight that when automated reporting meets finely tuned AI adjustments, efficiency margins can improve by up to 30%. These companies have transformed operational frustrations into strategic advantages, using regression models that predict bottlenecks and adaptive mechanisms for dynamic report updates. Academic research further confirms the synergy between robust algorithms and manufacturing excellence, where a “human-in-the-loop” approach ensures that data integrity and operational insights are maintained.
Innovating with Next-Generation Tools
Cutting-edge technology is reshaping manufacturing automation. Start-ups and research labs are implementing large language models to create bespoke solutions, such as email response automation and forecast adjustments, to further streamline operations. With continuous, iterative fine-tuning cycles demonstrated to reduce error rates by up to 25%, these innovations ensure both speed and quality. The strategic blending of automation with human oversight enables local experts to validate AI outputs, preserving data accuracy and unearthing insights that machines alone might overlook.
Speed and Reporting: Metrics in Motion
Enhancing report speed is critical for maintaining competitive advantage. The table below encapsulates key performance metrics before and after implementing advanced reporting solutions, offering a concrete view of the progress made in operational speed.
Metric | Pre-Implementation | Post-Implementation |
---|---|---|
Report Generation Time | 45 minutes | 20 minutes |
Error Rate | 8% | 3% |
Revision Frequency | 5 per week | 2 per week |
Report Accuracy | 85% | 95% |
The above table reflects tangible performance enhancements and serves as a benchmark for similar manufacturing operations seeking efficiency improvements. Keywords: report automation, efficiency metrics, manufacturing KPI. |
Fine-Tuning: Optimizing Manufacturing Levers
Beyond just speed, refining operations through fine-tuning is paramount. Below are key buzz concepts critical to understanding the nuances of operational adjustments:
- Throughput Lag
- A delay between the commencement and completion of production cycles, often mitigated by real-time monitoring and dynamic scheduling.
- Model Drift
- The gradual deviation of a predictive model’s performance, necessitating periodic recalibration to retain accuracy.
- Cycle Time Compression
- The reduction of time required to complete production cycles, achieved through targeted improvements in process workflows and technology adoption.
These elements underscore the importance of meticulous fine-tuning, as manufacturing operations evolve in complexity and speed. Emphasizing a balanced integration of AI with human expertise ensures that operational decisions are both rapid and robust.
Conclusion and Invitation for Reflection
The journey towards agile reporting and automated decision-making is ongoing, but the industry has begun to realize measurable improvements in both speed and process ownership. Manufacturing professionals are invited to reflect on their own efficiency challenges—particularly around rapid report generation and strategic fine-tuning. Can advanced AI strategies be seamlessly integrated while maintaining operational control? The experiences of industry leaders demonstrate that achieving this balance not only drives efficiency but also paves the way for continued innovation.
Engage with these methodologies and explore opportunities to optimize your own systems; the path to breakthrough performance is a continuous process of learning, iterative improvements, and peer collaboration.
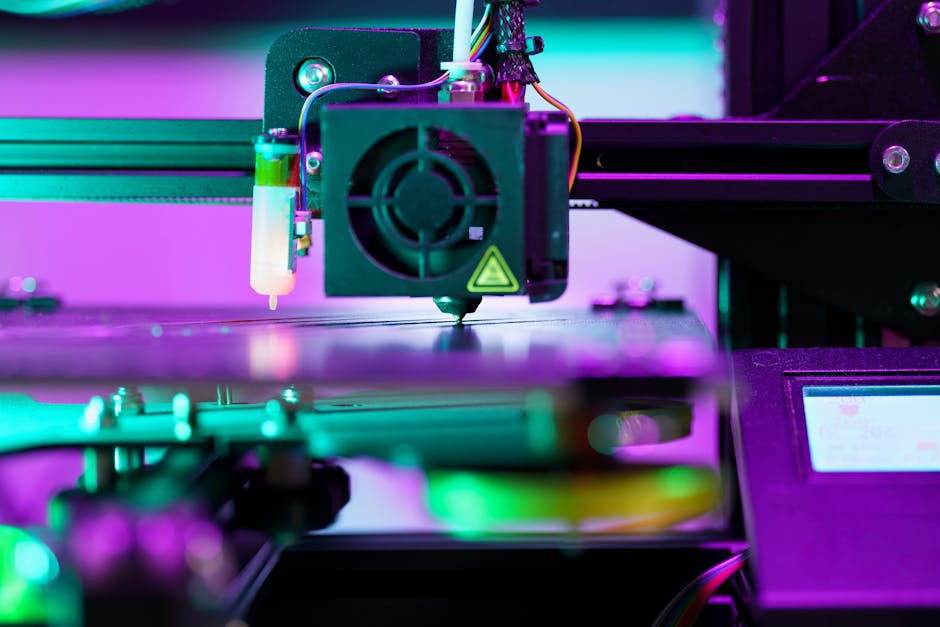