OPTIMIZATION STRATEGIES
Introduction
This guide explains how integrating real-time data analysis with continuous feedback loops can optimize manufacturing workflows. Drawing from emerging SQL query techniques and green manufacturing practices, the framework provides a comprehensive plan for iterative evaluations and continuous learning. Real-time decision-making and regular reviews have long been the backbone of resilient operations in the industry.
Real-Time Data Analysis as the Foundation
Effective workflow coordination relies on monitoring live production metrics. Systems that funnel actionable data mirror the practices used in automated reporting, enabling managers to quickly reconcile data across sources and make timely decisions. Historical industrial transitions demonstrate how accurate measurement and rapid response transform operational efficiency.
Feedback Loops and Iterative Evaluation Processes
Continuous improvement is achieved through feedback loops similar to the concepts in reinforcement learning. By regularly reviewing performance data, teams can adjust operations proactively—making optimization an ongoing evolution rather than a one-time event.
Technical Integration and SQL-to-Prompt Pipelines
Bridging data analysis with actionable insights requires robust technical integration. The guide highlights the role of SQL-to-prompt pipelines in triggering automated reporting tools. Such systems enable dashboards to initiate real-time queries during quarterly reviews, ensuring that technical precision supports cross-departmental operations and improves data reconciliation.
Cross-Departmental Communication and Collaborative Strategy
Manufacturing efficiency hinges not only on data but also on robust communication across departments like design engineering and production management. Historical innovations driven by collaborative efforts emphasize that combining technical enhancements with interpersonal strategies yields the best results.
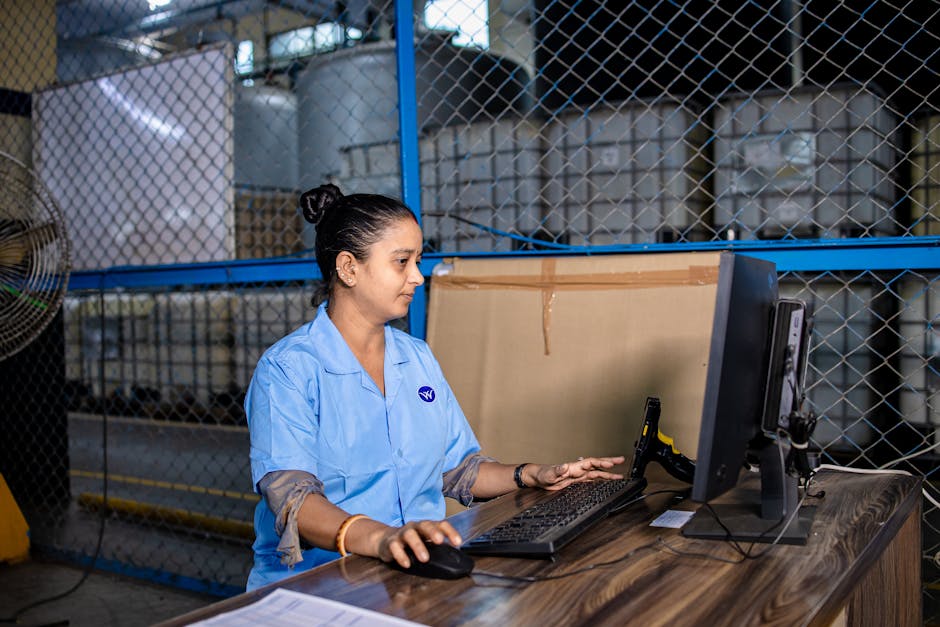
Key Terminology
- takt time
- A measure for syncing production pace with customer demand.
- kanban loops
- A system for visualizing work and managing inventory dynamically.
- SMED
- A methodology aimed at reducing changeover times in production.
Pre-Implementation vs. Post-Implementation Metrics
Metric | Before Optimization | After Optimization |
---|---|---|
Cycle Time | 120 sec | 90 sec |
Production Downtime | 15% | 8% |
Quality Rejection Rate | 5% | 2% |
Throughput Increase | 0% | 20% |
Considerations: Real-time data, iterative feedback, technical integration, and cross-department collaboration are key aspects. Keywords: reinforcement learning, SQL-to-prompt pipelines, and live production metrics. |
EVALUATION TACTICS
Case Studies and Lessons from Successful Workflow Optimization
Practical case studies illustrate how targeted evaluation tactics can transform operations. For instance, optimizing grinding processes through orthogonal experimental design and grey relational analysis has led to significant improvements. Analysis of before-and-after metrics shows that adjustments, such as fine-tuning production line timing, result in measurable efficiency gains.
Another example leveraged capacity optimization principles similar to those in advanced cloud resource management strategies. This case study demonstrates how well-planned technical evaluations and detailed data-led insights can enhance overall workflow performance.
Additional Technical Insights
Advanced SQL optimizations using indexed tables and materialized views have proven effective in reducing latency in real-time decision-making. Moreover, integrating sensor-driven data streams with automated alert systems enables proactive adjustments during operations reviews.

Key Terminology
- takt time
- An indicator used to gauge the rate of production in harmony with market demand.
- kanban loops
- A visual method to streamline process workflow and inventory control.
- SMED
- A technique focused on minimizing the time required for equipment changeovers.
Evaluation Summary
In summary, effective evaluation tactics revolve around comprehensive technical assessments, detailed data comparisons, and leveraging cross-functional insights. The documented case studies and advanced SQL optimizations underline the importance of continuous monitoring and adaptive strategies in achieving long-term manufacturing efficiency.