The manufacturing landscape is undergoing a radical transformation. Gone are the days when decisions were made on gut feeling. Today, precision-driven data visualizations offer clarity and direct guidance. Visionary companies such as General Electric and Siemens have embraced advanced dashboards to untangle complex data, moving away from cumbersome manual reconciliations.
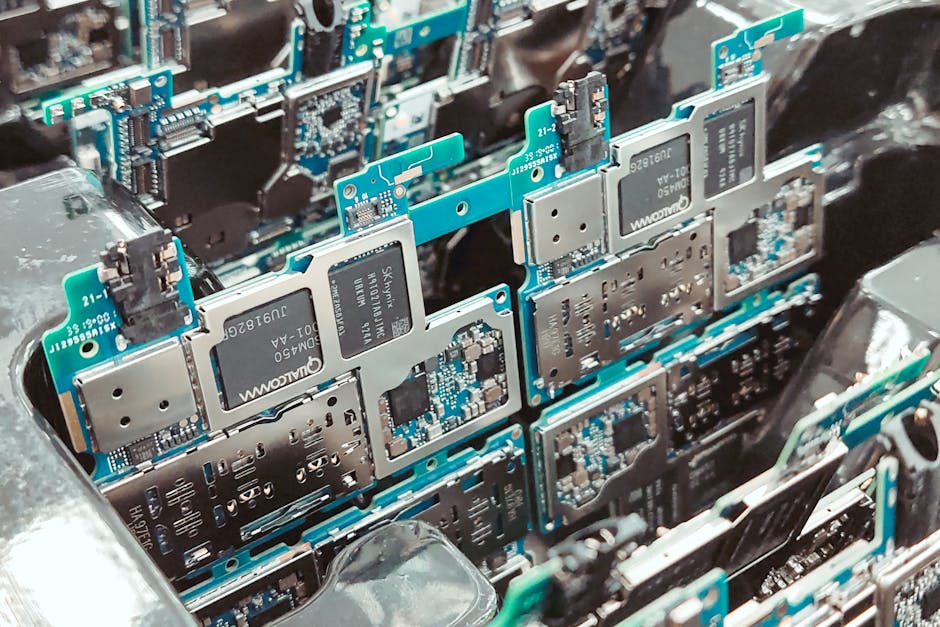
Manufacturers face challenges from data discrepancies and misaligned forecasts that can disrupt entire production lines. By leveraging real-time dashboards, hidden bottlenecks become visible and production forecasts are recalibrated. Metrics such as Overall Equipment Effectiveness (OEE) and production cycle times are transformed from raw statistics into actionable intelligence, ultimately enhancing production efficiency and reducing costs.
Metric | Raw Format | Visual Insight |
---|---|---|
Overall Equipment Effectiveness (OEE) | 90% | Optimized production floor operation |
Production Cycle Time | 45 mins | Enhanced throughput and reduced bottlenecks |
Downtime Frequency | High | Identified and minimized incidents |
Maintenance Alerts | Static Logs | Dynamic and predictive signals |
Using visual insights to compare key performance metrics is essential for identifying anomalies and aligning operational strategies. Keywords: visual dashboards, production insights, data clarity. |
Innovative manufacturers are turning challenges into opportunities. For example, a leading automotive parts supplier implemented a comprehensive dashboard strategy inspired by recent case studies. By integrating IoT data streams and AI analytics, the supplier achieved immediate visibility into production processes, driving down downtime and improving overall equipment effectiveness. This transition from reactive repairs to predictive maintenance schedules has been vital in maintaining a competitive edge.
Additional Real-World Examples
Beyond automotive parts, industries from consumer electronics to food processing are leveraging these advanced dashboards. The immediate availability of operational data allows teams to quickly reassign resources, resolve emerging bottlenecks, and continuously improve productivity. This dynamic approach has proven especially beneficial in hybrid work environments, where real-time updates and remote collaboration define the modern operations model.
Modern dashboards now break down intricate manufacturing metrics into digestible visuals. Automated data normalization aligns current production trends with historical data to form a robust single source of truth. This alignment empowers managers to isolate production hiccups with surgical precision and swiftly reallocate resources. With advanced integration, every chart, graph, and metric plays a direct role in streamlining operations, replacing outdated loops with efficient, automated alternatives reminiscent of Praxie’s transformative case studies.

This data-driven approach is not a temporary trend—it is the foundation upon which the future of manufacturing will be built. Adopting visualization-fueled practices is reshaping manufacturing operations. The transition to intelligent, data-informed production processes promises long-term benefits, including sustained efficiency gains, cost reductions, and a lasting legacy of operational excellence. As the era of digital transformation continues, each production cycle contributes to a narrative of innovation and precision.
- DATA-DRIVEN MANUFACTURING
- This is the shift from traditional production methods to precision-based decision-making using advanced data insights and visualization tools.
- KPI (Key Performance Indicators)
- Metrics that help evaluate the success or efficiency of production processes by tracking performance in real-time.
- Overall Equipment Effectiveness (OEE)
- A comprehensive standard measuring manufacturing productivity, combining availability, performance, and quality metrics to guide improvements.
- PREDICTIVE MAINTENANCE
- Techniques aimed at determining equipment conditions in real time to predict and prevent downtime, ensuring continuous production.
- THROUGHPUT BOTTLENECKS
- Critical limitations in production flow that hinder overall efficiency and require targeted visual data analysis to overcome.
- OEE DRIFT
- Subtle deviations in performance data over time that may indicate emerging issues requiring corrective action.
- SHADOW DOWNTIME
- Untracked periods of reduced production efficiency that can significantly impact overall output if not visualized and addressed.