Power Through: The Automation Mindset
A recent analysis makes it clear that there is no room for half measures. Precise forecasting demands a systemic shift toward full automation. Rather than expecting marginal gains from occasional tweaks, successful operations require a structured, step-by-step strategy.
Automation Strategies in Manufacturing
By deploying automated workflows that integrate seamlessly with manufacturing-specific systems such as MES (Manufacturing Execution Systems) and SCADA (Supervisory Control and Data Acquisition), operations professionals can revolutionize plant floor-to-dashboard data transfer. This approach creates reliable data pipelines and alert mechanisms that boost efficiency and intercept issues before they escalate.
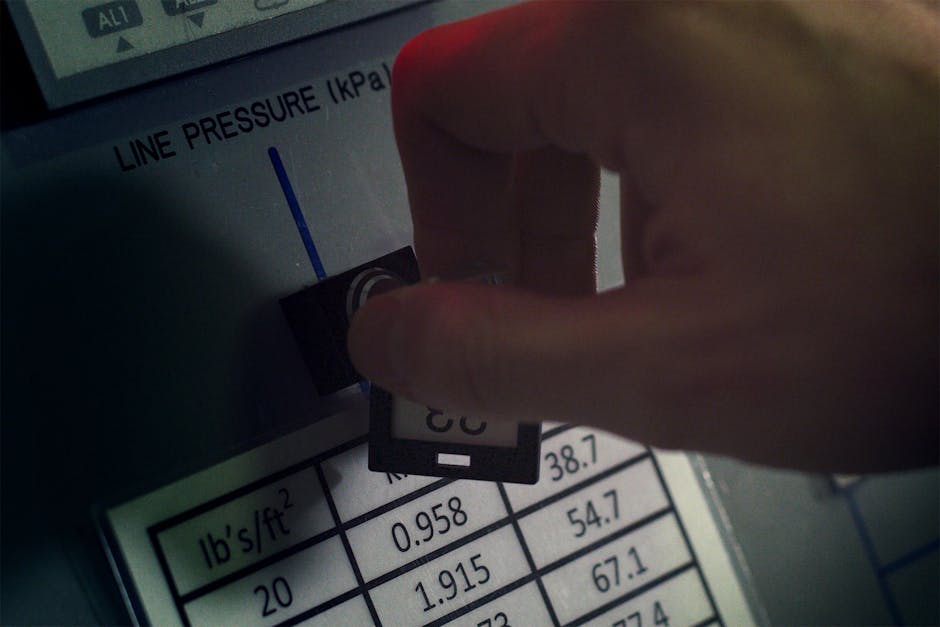
Enhancing Data Accuracy with Real-Time Adjustments
Historical missteps show that even giant firms have struggled with delayed data revisions and forecast inaccuracies. With edge computing technologies, companies can ensure data is adjusted in real time, eliminating lag and sharpening forecast precision. Consistently accurate inputs are crucial to stay ahead in competitive markets.
Integrating AI Tools for Predictive Maintenance
Industry experts on platforms like LinkedIn have advocated hyper-automation—using AI to infuse intelligence into forecasting processes. Tools that incorporate natural language processing analyze maintenance logs and equipment performance reports. This strategy not only optimizes projections but also provides a pre-emptive flag for potential downtime, ensuring that predictive maintenance becomes a seamless part of daily operations.
Comparing Manual and Automated Operations
Metric | Manual Approach | Automated Operations |
---|---|---|
Data Accuracy | Prone to human error | Consistently high reliability |
Response Time | Delayed adjustments | Real-time toggling |
Forecast Precision | Limited by manual tweaks | Enhanced through AI integration |
Operational Efficiency | High risk of process bottlenecks | Smooth, structured workflow |
Considerations: legacy systems may show failure points that are eliminated through modern automation; keywords include "real-time data", "predictive maintenance", "edge computing", and "MES/SCADA integration". |
Monitoring KPIs for Continuous Improvement
The backbone of a predictive and responsive operations strategy is the constant monitoring of key performance indicators (KPIs). These include cycle time, defect rates, and throughput lag. By setting clear thresholds and a no-nonsense monitoring regime, companies can ensure their automated systems deliver consistent results that keep pace with rapid operational shifts.
Key Operational Terms and Insider Insights
- Throughput Lag
- A delay between data generation on the plant floor and its reflection in forecasting models. Minimizing this lag is key to accurate, real-time decision making.
- Forecast Drift
- The gradual deviation of predictions from actual performance due to outdated data inputs or infrequent updates.
- Ops Sync Debt
- A measure of accumulated inefficiencies when legacy systems fail to communicate or align with modern, automated processes.
These industry-driven terms represent the hurdles that legacy workflows present. Addressing them through automation is not just an upgrade—it’s a complete transformation of the operational paradigm.